Wtryskiwanie
Na czym polega wtryskiwanie?
Wtryskiwanie tworzyw sztucznych to bardzo wydajna technologia pozwalająca na wielkoseryjną produkcję wyrobów. Metoda wtrysku polega na uplastycznieniu granulatu tworzywowego pod wpływem wysokiej temperatury. Uplastycznione tworzywo wtryskiwane jest pod ciśnieniem do formy, w której zestala się w wypraskę. Podczas wtrysku powstaje wyrób lub – w przypadku detali złożonych – część wyrobu, która potem podlega montażowi.
Formowanie wyrobu (wtryskiwanie) to najważniejsza część całego procesu. To właśnie w gnieździe formy wtryskowej tworzy się jego kształt geometryczny i kształtują własności użytkowe. Wtryskiwanie składa się z trzech zasadniczych etapów:
- Faza wtrysku: zaprogramowana porcja tworzywa sztucznego wtłoczona zostaje z zadaną prędkością do gniazda formy. Po wypełnieniu matrycy następuje gwałtowny wzrost ciśnienia i sprężenie masy.
- Faza docisku: następuje dalszy dopływ tworzywa do gniazda formy, dzięki czemu uzupełniane są wolno następujące ubytki skurczowe masy. Ten etap wtryskiwania trwa tak długo, aż nie nastąpi zakrzepnięcie lub zamknięcie drogi przepływu.
- Faza chłodzenia: zaczyna się natychmiast po wypełnieniu gniazda i trwa do chwili usunięcia wypraski z formy.
Wtryskiwanie to technologia przetwarzania tworzyw sztucznych i produkcji szerokiego spektrum wyrobów od drobnych detali aż po całe panele karoserii samochodów.
Produkcja na wtryskarkach – wtryskiwanie
Posiadamy wtryskarki sterowane numerycznie o sile zwarcia do 120T. Aby móc świadczyć kompleksowe usługi w trakcie produkcji korzystamy ze specjalnych urządzeń peryferyjnych takich jak: dozowniki barwnika i dodatków do tworzyw sztucznych, mieszadła, suszarki, dodatkowe systemy chłodzące, które gwarantują uzyskanie produktu w 100% zgodnego z wytycznymi – także w przypadku produkcji wielkoseryjnej.
Maksymalna objętość i gramatura wtryskiwanego surowca wynosi odpowiednio, w zależności od zastosowanego tworzywa, 200 cm³ i 190 g (maksymalne wartości podane są dla polistyrenu).
Maksymalna wielkość stosowanych form to: wysokość – 450 mm, długość i szerokość – 400 mm.
Stosowane przez nas tworzywa do produkcji to:
- polipropyleny PP,
- polietyleny (LDPE, HDPE),
- polistyreny PS,
- elastomery termoplastyczne (TPE),
- polichlorki winylu (PVC).
Jako doświadczony producent wyrobów z tworzyw sztucznych korzystamy wyłącznie ze sprawdzonych dostawców wysokiej jakości surowców, także tych dopuszczonych do kontaktu z żywnością lub posiadających odpowiednie certyfikaty, konieczne przy produkcji wyrobów medycznych. Zaufały nam firmy medyczne oraz kosmetyczne, a to najlepsza rekomendacja, potwierdzająca najwyższą jakość produktów wytwarzanych w KINEI.
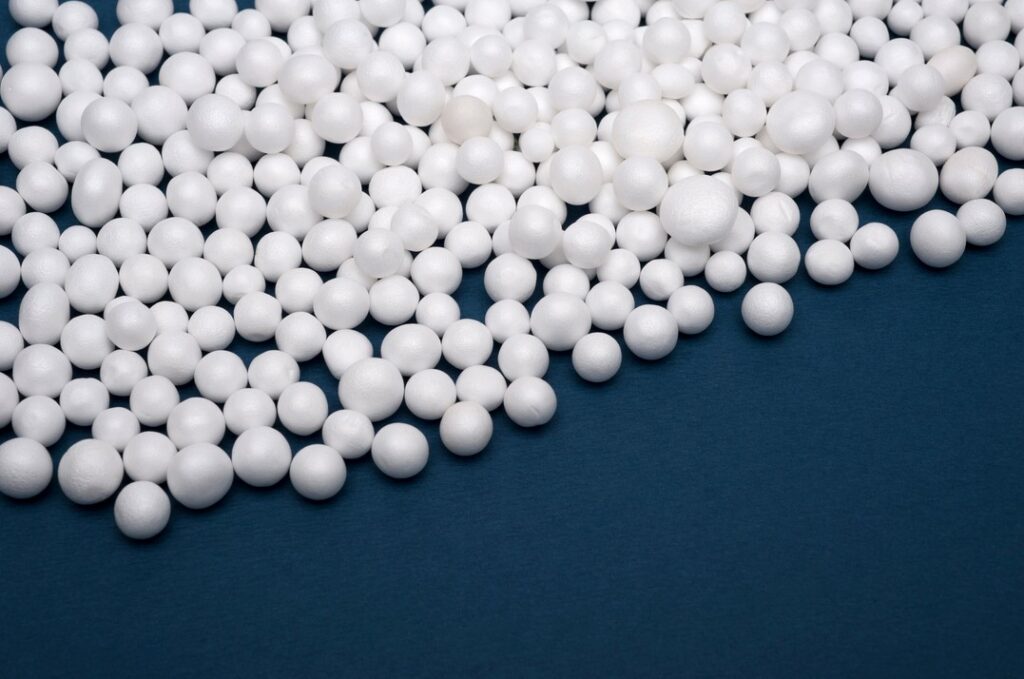
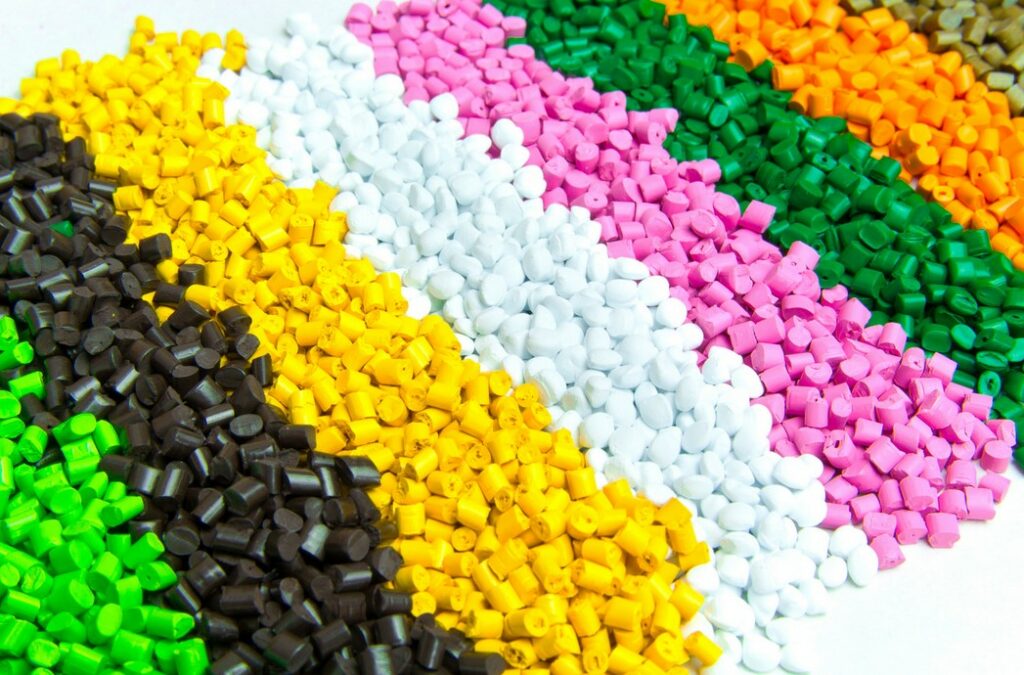
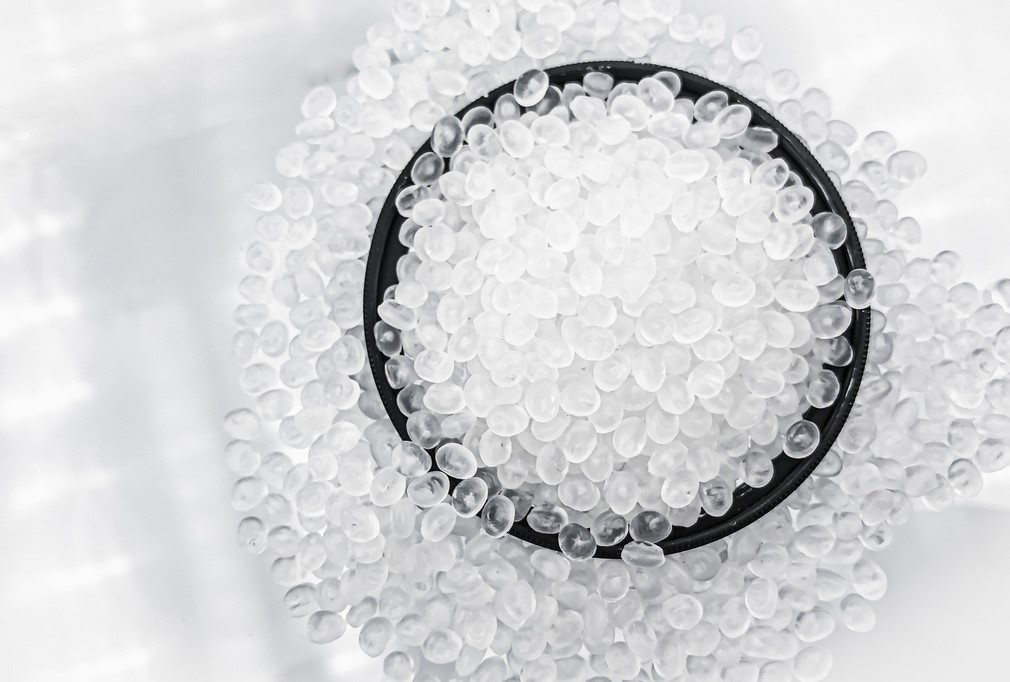
Wtryskiwanie – wysoka jakość produkcji i ochrona środowiska
Technologie wtrysku pozwalają nam na wytwarzanie wyrobów niezawodnych, trwałych, a przede wszystkim stosunkowo tanich w zakupie. Dodatkowo dbamy o środowisko, nie tylko w przekazie marketingowym. Cały odpad poprodukcyjny (na przykład przy produkcji o standardzie czystości farmaceutycznym) mielimy i wykorzystujemy powtórnie przy opakowaniach, które nie mają aż tak wysokich wymagań czystości. Naszym klientom udostępniamy skład mieszanki tak, by cały proces był w pełni transparentny. Przez wszystkie lata działalności udało się nam osiągnąć niemal zerowy poziom zwrotów i reklamacji!
Elementy wytwarzane w technologii wtrysku
Możliwe do uzyskania wymiary produktów – detale małogramowe o masie 1–3g oraz opakowania o pojemności maksymalnej 5L. Pozostałe typy produktów zgodnie z obsługiwanymi wielkościami form oraz koniecznej sile zwarcia.
Maksymalne wymiary i wielkości
- maksymalna objętość i gramatura wyrobu: 200 cm3 i 190 g
- maksymalna obsługiwana wielkość formy wtryskowej to 400 x 400 x 450 mm
Co ważne obsługujemy zarówno zamówienia krótkoseryjne jak i wieloletnie. Działamy zgodnie z zasadą „turnkey” – w razie potrzeby zapewniamy produkcję i montaż, a także pakowanie oraz transport na terenie całej Europy.
Przykładowe wyroby realizowane w metodzie formowania wtryskowego:
- kontrolki, oprawy bezpiecznikowe, układy,
- opakowania i pojemniki medyczne/spożywcze
- obudowy, osłony
- separatory, filtry bębnowe
- kasetki na leki,
- kubeczki, pudełka na maści i kremy,
- opakowania w kształcie tuby,
- strzykawki, zakraplacze, pipety, zakrętki,
- osłony, spinki, podstawki, zębatki, ograniczniki, odboje,
- zaworki, ustniki, korki, kształtki,
- detale techniczne, wtyczki, łączniki, kolanka, uchwyty
- sztućce,
- zabawki, klocki
- wiaderka, skrzynki rewizyjne
- części, akcesoria samochodowe i wiele innych.
Formowanie wtryskowe – jak przebieg proces wtryskiwania?
Produkcja z tworzyw sztucznych na wtryskarkach składa się z kilku faz, które precyzyjnie określają jej przebieg. Dlatego też dzielimy je na dwie kategorie:
- Fazy mechaniczne: określają przebieg ruchów i obciążeń wtryskarki. Są to kolejno zamykanie formy, dojazd i odjazd agregatu wtryskowego, otwieranie i zamykanie formy oraz samo wypychanie wypraski. Dodatkowo zaliczamy do nich także wszelkie przerwy, które mają miejsce w trakcie produkcji danego detalu. Wówczas najczęściej mają miejsce dodatkowe czynności obsługi formy wtryskowej.
- Fazy technologiczne: określają zmiany stanu tworzywa w cylindrze wtryskarki i przebiegi zjawisk zachodzących już w samej formie. To one decydują o finalnym kształcie, a nawet właściwościach elementu. Kolejność faz technologicznych jest ściśle określona. Podsumowując warto dodać, że obecnie znanych jest niemal 30 odmian technologicznych procesów wtryskiwania tworzywa sztucznego.
Fazy technologiczne wtrysku
Najistotniejszy z punktu widzenia technologicznego opis procesów przejścia tworzywa sztucznego w konkretny detal
Faza wtrysku: gniazdo lub gniazda formy są wypełniane tworzywem sztucznym pod dużym ciśnieniem pozwalającym na pokonanie oporów fizycznych. Dodając do tego odpowiednio zaprogramowaną prędkość wtryskiwania otrzymujemy wypraskę o żądanym kształcie.
- Faza sprężania: w wyniku gwałtownego wzrostu ciśnienia w momencie całkowitego wypełnienia formy wtryskowej następuje dokładne odwzorowanie kształtu gniazda.
- Faza docisku: podczas chłodzenia tworzywa dochodzi do silnego skurczu objętościowego, który w opisywanej fazie kompensowany jest materiałem pozostałym w cylindrze wtryskarki.
- Faza chłodzenia: rozpoczyna się już w trakcie fazy docisku. Pozwala na ochłodzenie wypraski do temperatury umożliwiającej bezpieczne usunięcie jej z formy. W niektórych przypadkach konieczne jest zastosowanie dodatkowego chłodzenia, np. wodnego.
- Faza uplastyczniania: ślimak dozujący pobiera zadaną ilość granulatu, ogrzewa go i stapia, równocześnie przemieszczając go na czoło ślimaka. Gdy nastawiona droga dozowania zostaje osiągnięta wtryskarka jest gotowa do rozpoczęcia kolejnego cyklu pracy.
Jakie tworzywa można wtryskiwać?
Tworzywa używane do formowania wtryskowego to wciąż najmłodsza, zupełnie odrębna i najbardziej dynamicznie rozwijająca się grupa materiałowa. Roczna produkcja tworzyw sztucznych już 10 lat temu była dwukrotnie wyższa niż produkcja stali. Produktem wyjściowym każdego tworzywa jest jego chemicznie czysta postać w postaci polimeru. Tworzywo, które faktycznie jest przetwarzane we wtryskarce to najczęściej połączenie polimeru i kilku innych dodatków:
TWORZYWO SZTUCZNE = polimer + dodatki modyfikujące + napełniacze
Co ciekawe polimery zbudowane są podobnie do organicznych materiałów naturalnych, takich jak drewno, czy wełna. Właściwości poszczególnych typów tworzyw i ich odmian różnią się od siebie w zależności od:
- składu chemicznego i budowy makrocząsteczek
- zastosowania stabilizatorów, środków zmiękczających
- dodatku napełniaczy w różnej postaci i różnych ilościach, np. włókien szklanych, mineralnych lub węglowych, kredy, grafitu, pigmentów, barwników
- dodatków środków utrudniających palność, antystatyków i innych.
Formownie wtryskowe – tworzywa termoplastyczne
Do produkcji elementów z tworzyw sztucznych najczęściej wykorzystuje się tworzywa termoplastyczne, których cechą charakterystyczną jest możliwość wielokrotnego przetwarzania. W zależności od rodzaju i budowy, tworzywa najczęściej w postaci granulatu są najpierw podgrzewane w cylindrze wtryskarki, mieszane z dodatkami, a następnie pod wysokim ciśnieniem sprężane i z zadaną prędkością przemieszczane w formie. Podczas chłodzenia w formie utrwala się bryła elementu lub wykształca się w niej struktura krystaliczna.
Tworzywa termoplastyczne dzielą się na trzy podstawowe grupy:
- o budowie amorficznej takie jak: polistyren (PS) oraz jego pochodne PMMA, CA, PPO, PVC, PC, PAA, PSU, PES, czy tworzywa fluorowe
- o strukturze częściowo krystalicznej takie jak: PL LD, PA, EVA, PP, PE, HD, POM, PPS, PER, PBT
- termoplastyczne: TPE, często mieszane z PP, np dla zwiększenia ich udarności
Wtryskiwanie polietylenu
Polietylen (PE) uzyskiwany w procesie polimeryzacji etylenu pomimo, iż posiada bardzo prostą strukturę polimeru jest tworzywem najczęściej wykorzystywanym przy produkcji wtryskowej. Głównymi cechami polietylenu, które mają wpływ na jego gigantyczną popularność w przemyśle przetwórstwa tworzyw sztucznych są:
- niska cena
- znakomita izolacja elektryczna w szerokim zakresie częstotliwości
- duża odporność chemiczna
- wysoka wytrzymałość i elastyczność
- możliwa do uzyskania przezroczystość
Polietylen wyewoluował do dwóch najczęściej używanych form LDPE oraz HDPE. Dominacja polietylenu wynika z faktu, iż oferuje on najszerszą kombinację charakterystyk, m.in. płynięcia czy stabilności termicznej, które są pożądane w opisywanych procesach produkcyjnych.
Formowanie wtryskowe polietylenu najszerzej wykorzystuje się przy produkcji opakowań, zwłaszcza w farmacji oraz kosmetologii. Inne branże wykorzystujące ten polimer to m.in. budowlana, transportowa, elektryczna i rekreacyjna. Rozwój technologii ciągle poprawia funkcjonalność polietylenu, czyniąc go najbardziej wydajnym sposobem wykorzystania zasobów naturalnych. Dodatkowo dzięki nowoczesnym technologiom możliwe jest przetwarzanie raz zużytych opakowań oraz wykorzystanie odpadu produkcyjnego.
Jak działają wtryskarki?
Działanie wtryskarki
Działanie wtryskarki polega na podgrzaniu tworzywa sztucznego w postaci granulowanej do temperatury topnienia, a następnie wtłoczeniu płynnego już tworzywa do formy pod bardzo dużym ciśnieniem. Forma nadaje ostateczny kształt wyrobu, a dzięki chłodzeniu surowiec zastyga i może zostać zdjęty z matrycy i wyjęty z wtryskarki.