Rotomoulding – odlewanie rotacyjne
Rotomoulding – metoda rotacyjna polega na obrotowym, odśrodkowym odlewaniu wyrobu w formie. Maszyna do rotoformowania obraca się jednocześnie w dwóch osiach, dzięki czemu podgrzewanie w czasie jednego cyklu pracy tworzywo równomiernie rozkłada się po ściankach formy. Co ważne w kontekście całego procesu, forma obraca się także po zatrzymaniu podgrzewania. Olbrzymią zaletą produkcji w rotomouldingu jest możliwość przygotowania wyrobów jednoelementowych, co przekłada się w istotnym stopniu na ich trwałość.
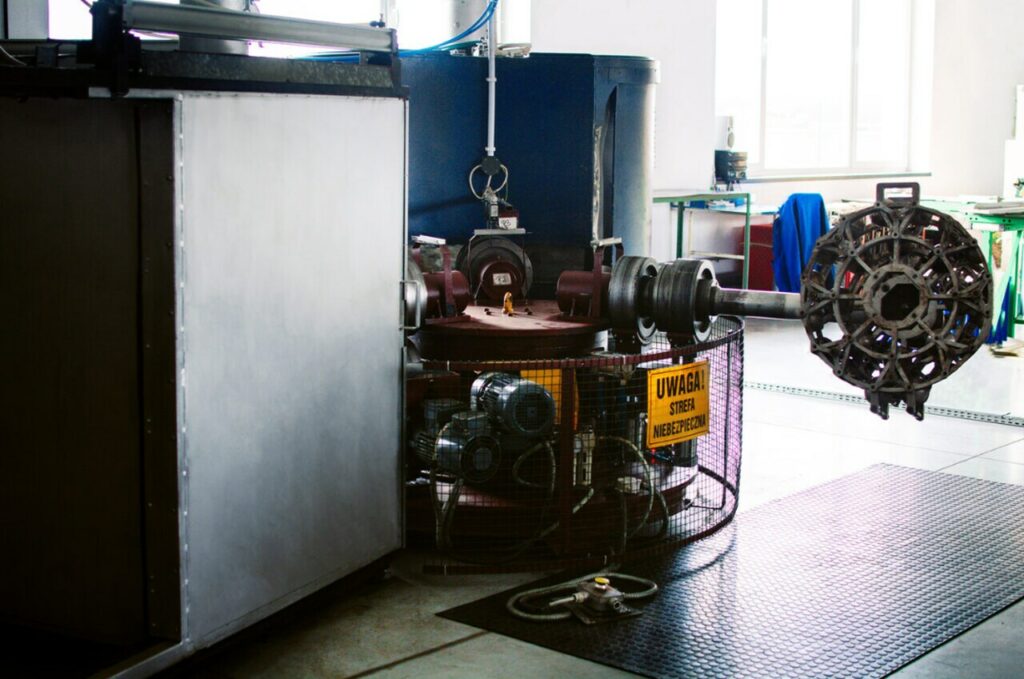
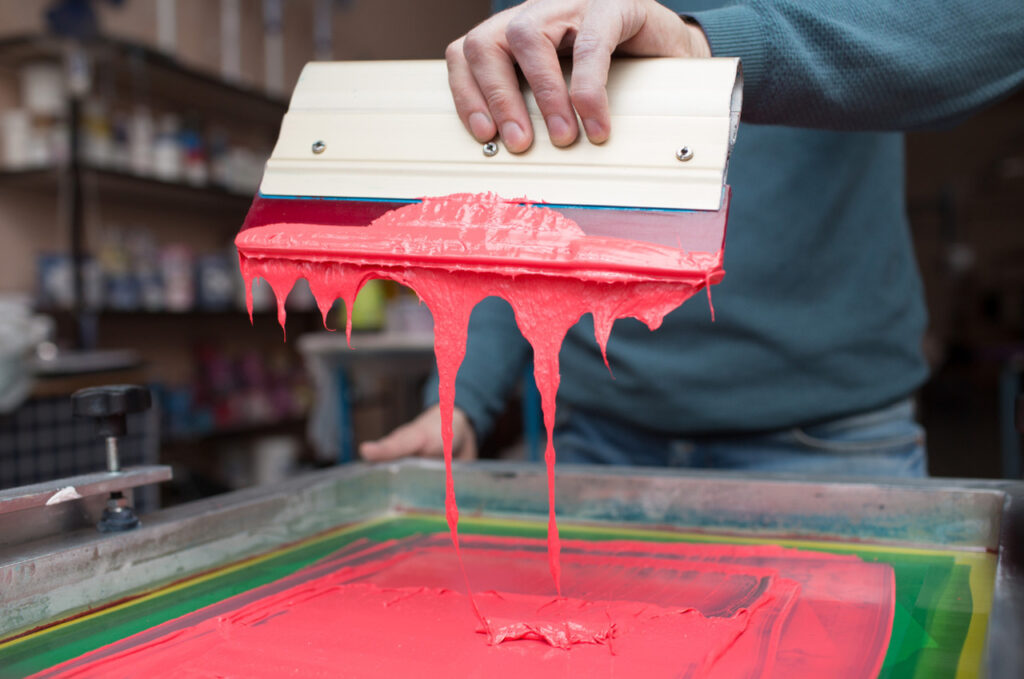
Rotomoulding – etapy i charakterystyka procesu
Rotomoulding to wyjątkowa technologia, którą w pewnym uproszczeniu można opisać jako polegającą na odlewaniu odśrodkowym. Forma napełniana jest tworzywem w postaci płynnej lub proszkowej w zależności od wyrobu. Po zamknięciu formy poprzez jej podgrzanie i obracanie w dwóch prostopadłych płaszczyznach następuje odpowiednio dla postaci płynnej żelowanie tworzywa, natomiast proszkowej jego polimeryzacja. Po zakończeniu tych procesów formę chłodzi się i wyjmuje gotowy wyrób. Formy do produkcji tą metodą składają się zwykle z dwóch lub jednej części. Metodą rotacyjną możemy otrzymywać przedmioty całkowicie zamknięte, puste w środku o bardzo dużej wytrzymałości, odporności na uszkodzenia i sztywności.
Zalety produkcji w technologii rotoformowania
- możliwość tworzenia produktów o bardzo skomplikowanym kształcie
- pomijalne straty materiału w procesie produkcyjnym
- bardzo wysoka powtarzalność wyrobów
- niskie koszty form i produkcji
- brak konieczności tworzenia elementów składowych wyrobu i późniejszego ich łączenia
- bardzo wysoka sztywność i wytrzymałość produktów
- możliwość przygotowania krótkich serii przedmiotów przy zachowaniu niskich kosztów
- w wyrobie można umieścić elementy metalowe, np. wkładki z gwintem
W naszym przypadku maksymalne wyroby, które możemy wyprodukować (zależnie od kształtu) mogą mieć podstawę o średnicy 1000 mm i wysokość 500-900 mm.
Przykładowe wyroby realizowane w metodzie rotomouldingu:
- gruszki medyczne,
- piłki rehabilitacyjne i gimnastyczne,
- akcesoria dla ratowników wodnych, boje ratownicze i cumownicze,
- zabawki takie jak: huśtawki, zabawki na biegunach, zjeżdżalnie, baseny, kulki,
- odbojniki,
- poduszki rehabilitacyjne,
- roboty,
- słupki i pachołki,
- separatory ruchu, znaki drogowe,
- zbiorniki na wodę i paliwo,
- obudowy, osłony,
- produkty ogrodnicze, płotki,
- meble.
Co ważne, zaprojektowanie i wykonanie jednej formy pozwala na wprowadzanie pewnych modyfikacji w obrębie wytwarzanego produktu bez konieczności jej zmiany. Możliwa jest między innymi zmiana koloru, czy nadruk odpowiednich grafik bądź napisów.
Nowoczesna metoda rotomoulingu pozwala na znaczne ograniczenie kosztów projektowych, zwłaszcza w przypadku małoseryjnych produkcji. Jednocześnie dzięki swojej wysokiej wydajności, niewielkim stratom, jakie generuje oraz niezawodności dobrze sprawdza się także przy produkcjach rzędu setek tysięcy elementów rocznie.
Rotomoulding – tajniki technologii odlewania rotacyjnego
Rotomoulding jako technologia przetwarzania tworzyw sztucznych wciąż jeszcze jest stosunkowo mało znana. Tymczasem rotoformowanie umożliwia produkowanie wyjątkowo wytrzymałych wyrobów, które są szeroko wykorzystywane w niezliczonej ilości branż.
Materiał na odlewy z plastiku
W odlewaniu rotacyjnym najczęściej z uwagi na swoje parametry używa się materiałów z rodziny PE (polietyleny). Do najpopularniejszych rodzajów należą:
- LDPE – polietylen o niskiej gęstości w kolorze mlecznobiałym
- HDPE – polietylen o wysokiej gęstości, mniej przezroczysty
- LLDPE – niskociśnieniowy liniowy polietylen o niskiej gęstości
- PVC – związki plastizoli z polichlorku winylu, nylony i polipropylen
- PEX – polietylen sieciowany, stosowany głównie do produkcji rur i izolacji, gdyż nie jest odwracalnie termoplastyczny
- Przemiał – odpady z innych procesów produkcyjnych, dla wyrobów o niskich wymaganiach jakościowych (recykling)
W KINEI specjalizujemy się właśnie w nieco rzadziej stosowanych tworzywach PVC. Produkcja elementów ze związków plastizoli wymaga przede wszystkim zaawansowanej wiedzy chemicznej. W przeciwieństwie do innych wymienionych materiałów, związki polichlorku winylu wymagają opracowania specjalnej receptury w zależności od ich parametrów i wymagań stawianych finalnemu produktowi. Tak przygotowany surowiec, przechodzący wcześniej ścisłą kontrolę jakości jest mieszany, wykonywane są próby jakościowe, a następnie finalna produkcja. Produkty wytwarzane w KINEI często mają zastosowanie medyczne, a co za tym idzie surowce i finalny skład wyrobów muszą przejść bardzo wymagające badania.